In order to reduce faults, it is necessary to accurately detect the voltage, current, and temperature of the battery, preprocess the results, calculate the state of charge and operating state, send the results to the engine control unit (ECU), and control the charging function.
Modern cars were born in the early 20th century. The first car relied on manual start-up, which required a great deal of strength and was highly risky. The car's "hand crank" caused many deaths. In 1902, the first battery starter motor was successfully developed. By 1920, all cars had been started using electricity.
The initial use was dry batteries, which had to be replaced when power was exhausted. Shortly afterwards, liquid batteries (ie, ancient lead-acid batteries) replaced dry batteries. The advantage of a lead-acid battery is that it can be recharged when the engine is working.
In the last century, there was little change in lead-acid batteries, and the last major improvement was to seal it. What really changes is the demand for it. Initially, the battery was used only to start the car, honking and powering the lights. Today, before the ignition, all of the car's electrical systems are powered by it.
The proliferation of new electronic devices is not just consumer electronics devices such as GPS and DVD players. Today, body electronics such as engine control units (ECUs), power windows, and power seats are standard on many basic models. The exponentially increasing load has had a serious impact, as evidenced by the increasing number of failures caused by electrical systems. According to ADAC and RAC statistics, almost 36% of all vehicle faults can be attributed to electrical faults. If this number is analyzed, it can be found that more than 50% of failures are caused by the lead-acid battery component.
Assess battery health The following two key features reflect the health of a lead-acid battery:
(1) State of Charge (SoC): The SoC indicates how much charge the battery can provide, expressed as a percentage of the battery's rated capacity (ie, the SoC of the new battery).
(2) Operating status (SoH): SoH indicates how much charge the battery can store.
The state of charge indicates that the state of charge is like the "fuel gauge" of the battery. There are many ways to calculate SoCs, of which the most common ones are two: open circuit voltage measurement and coulomb measurement (also known as coulomb counting).
(1) Open-circuit voltage (VOC) measurement method: A linear relationship between the open-circuit voltage of the battery when it is unloaded and its charge state. There are two basic limitations to this calculation:
One is that in order to calculate the SoC, the battery must be open circuited and not connected to the load; the second is that this measurement is only accurate after a fairly long stabilization period.
These limitations make the VOC method unsuitable for online SoC calculations. This method is usually used in a car repair shop, where the battery is removed and the voltage between the positive and negative electrodes of the battery can be measured with a voltmeter.
(2) Coulomb assay: This method uses Coulomb counting to integrate the current versus time to determine the SoC. With this method, the SoC can be calculated in real time even if the battery is under load conditions. However, the coulomb assay error increases over time.
Generally, the open circuit voltage and the coulomb counting method are used to calculate the state of charge of the battery.
The operating state operating state reflects the general state of the battery and its ability to store charge as compared to a new battery. Due to the nature of the battery itself, SoH calculations are very complex and rely on understanding the battery chemistry and the environment. The SoH of a battery is affected by many factors including charge acceptance, internal impedance, voltage, self-discharge, and temperature.
It is generally considered difficult to measure these factors in real time in an environment such as a car. During the start-up phase (engine start-up), the battery is under maximum load, which best reflects the battery's SoH.
The SoC and SoH calculation methods used by leading auto battery sensor developers such as Bosch and Hella are highly confidential and often protected by patents. As intellectual property owners, they often work closely with battery manufacturers such as Varta and Moll to develop these algorithms.
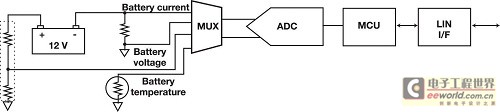
Figure 1 shows the discrete circuits commonly used for battery detection.
Figure 1 Discrete battery detection solution This circuit can be divided into three parts:
(1) Battery detection The battery voltage is detected by a resistive attenuator tapped directly from the positive pole of the battery. To detect the current, place a sense resistor (usually 100mΩ for a 12V application) between the negative pole of the battery and ground. In this configuration, the metal chassis of the vehicle is typically ground, and the sense resistor is installed in the battery's current loop. In other configurations, the negative pole of the battery is ground. For SoH calculations, the temperature of the battery must also be checked.
(2) Microcontrollers Microcontrollers or MCUs mainly perform two tasks. The first task is to process the result of an analog-to-digital converter (ADC). This may be as simple as performing only basic filtering, or it may be complex, such as computing SoCs and SoHs. The actual functionality depends on the processing power of the MCU and the needs of the car manufacturer. The second task is to send the processed data to the ECU via the communication interface.
(3) Communication Interface Currently, the Local Interconnect Network (LIN) interface is the most commonly used communication interface between the battery sensor and the ECU. LIN is a single-line, low-cost alternative to the well-known CAN protocol.
This is the simplest configuration for battery detection. However, most sophisticated battery detection algorithms require simultaneous sampling of battery voltage and current, or battery voltage, current, and temperature.
In order to perform simultaneous sampling, it is necessary to add at most two analog-to-digital converters. In addition, ADCs and MCUs need to regulate the power supply in order to work properly, resulting in increased circuit complexity. This has been solved by the LIN transceiver manufacturer by integrating the power supply.
The next step in automotive precision battery testing is the integration of ADCs, MCUs, and LIN transceivers, such as Analog Devices' ADuC703x family of precision analog microcontrollers.
The ADuC703x offers two or three 8 ksps, 16-bit sigma-delta ADCs, a 20.48 MHz ARM7TDMI MCU, and an integrated LIN v2.0-compliant transceiver.
The ADuC703x series integrates a low dropout regulator on-chip and can be powered directly from a lead-acid battery.
In order to meet automotive battery test requirements, the front end includes the following components: a voltage attenuator for monitoring the battery voltage; a programmable gain amplifier that, when used with a 100mΩ resistor, supports measurement of full-scale currents up to 1A to 1500A; And supports coulomb counting without software monitoring; and an on-chip temperature sensor.
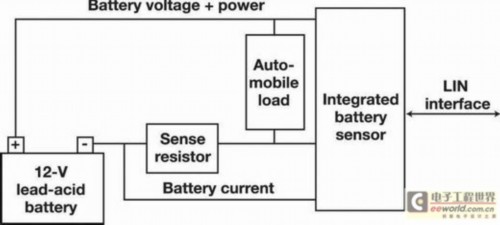
Figure 2 shows the solution using this integrated device.
Figure 2 Example of a solution using an integrated device A few years ago, only high-end cars were equipped with battery sensors. Nowadays, more and more mid-range and low-end cars are installed with small electronic devices, which was only seen in high-end models ten years ago. The number of failures caused by lead-acid batteries has consequently increased. Within a few years, battery sensors are installed in every car, thereby reducing the risk of increasing failure of electronic devices.
YF850 type water ripples Color equipment needed to produce the appearance of the roof based on a variety of production and yield. Building colorful, flowing lines , increase construction tone and beautify the urban landscape for the arched roof of the building.
Vaulted roof of the building features:
1, no no Tan Liang , tall open space , free to split combination , easy to use.
2 , light weight , steel is strong , good elasticity , excellent seismic performance.
3, the mechanical lock stitch seams , airtight , saving time and improving efficiency .
4 , by way of reasonable force , reserve safety , can withstand high wind loads and earthquake forces
5 , a variety of design styles , adaptable , either downtown district or remote town , economy and beautiful apply.
6 , scientific design ideas and advanced construction methods to make the whole building constructed dome color plates , the contact connections are very reasonable precision , so that the project quality assurance. Architectural appearance, diverse.
7 , large-span arched roof, shaped like a rainbow , Titaiqingying , giving a whole-hearted feeling of beauty .
8 , diverse architectural styles that can be used straight groove boards, and any combination of the traditional structure of the building into different forms , imaginative endless variations .
9 , can be built for different purposes and architecture , but also bagging between the two buildings , but also in the existing upstairs and floor, both solve the water problem and the increased use of space.
Ridge Cap Roll Forming Machine
Ridge Cap Roll Forming Machine,Ridge Tile Making Machine, Stainless Steel Pipe Making Machine, Steel Tube Making Machine
HEBEI YUFA TILE PRESS EQUIPMENT CO.,LTD. , http://www.china-rollformingmachinery.com